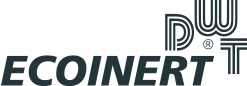
This website uses cookies and similar technologies!
Legislation allows cookies to be stored on your device if they are absolutely necessary for the operation of the website. For all other types of cookies, we require your consent (opt-in).
In addition, personal data is also collected and processed on our website, which is partially and exclusively forwarded to our partners for web analysis / statistics. The extent to which personal data is processed depends on your use of this website.
If you wish to continue using our site, please agree to the storage of cookies and the processing of personal data, select your personal setting or refuse in principle. If you refuse, only absolutely necessary data will be processed and stored. You can object to or adjust your consent at any time with effect for the future.
For more information on the storage and processing of personal data, please refer to our privacy policy.